Safety-related tactile sensor
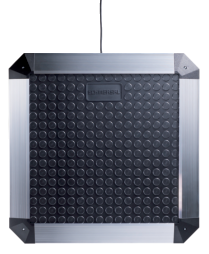
Safety mats
- Robust design
- Modular switching mat system
- Special sizes are available on request
- Maintenance free
- Simple mounting
- Slip-free surface
- High resistance to chemicals
- No additional terminating resistor required
- No additional baseplate
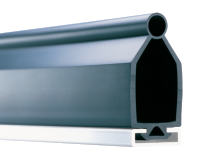
Safety edges
- Dirt and moisture in the profile are to a great extent compensated
- Insensitive to environmental conditions
SAFETY-RELATED TACTILE SENSORS
In some application areas, the use of tactile protective equipment which reacts to contact or pressure is recommended. Tactile sensors are used, for example, in lifting platforms, lift tables and movable shelf systems. Components to secure the surfaces of machines and industrial robots are also required. For these areas of application, Schmersal offers safety switch mats and switch strips, plus bumpers and switch cushions in various designs.SMS 4 / SMS 5 safety mats
Safety switch mats are often used to secure hazardous areas in punching systems, pipe benders and wood processing machines. In contrast to optoelectronic protection equipment such as safety light curtains and grids, safety switch mats allow the monitoring of entire working areas. As soon as someone steps on the switch mat, the hazardous movement is switched off via a connected safety relay module. Schmersal offers two ranges of safety mats.
Safety edges SE40 and SE70
When it comes to securing crushing and shearing points, safety edges are used. On contact, they stop hazardous movements and thus prevent injuries to persons and damage to machines. Typical areas of application for tactile sensors are warehouse lifts, lift doors, loading bridges and industrial gates. The safety edges consists of an aluminium profile strip, a rubber profile and slot-in sensors. They are not sensitive to environmental influences.
SAFETY BUMPERS SSG-SBL
Safety-related bumpers are protective equipment with a proximity function. They prevent hazards to persons if they approach a hazardous point, for example, by switching off, stopping or reprogramming a hazardous movement. An actuating force is applied to a signal transmitter and, in conjunction with an evaluation signal, generates a control command. Safety bumpers can be used in driverless transport systems, electric suspension railways, moving machine parts and on automatic sliding doors to secure crush and shear points, etc.
FURTHER INFORMATION ON TACTILE SENSORS IN THE ONLINE CATALOGUE
Interested parties who require further information on safety-related tactile sensors such as safety mats, safety edges and bumpers will find what they are looking for in the Schmersal Group's extensive online catalogue. Dimensions, information on chemical resistance, clear illustrations and various other general and mechanical data on the individual products can be viewed here.