Automation technology
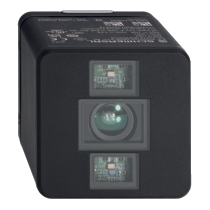
Cameras
- 3D camera
- Time-of-Flight Technologie (ToF)
- Use in manufacturing processes, logistics and robotics
- Standardised GenICam data interface
- Optimally adaptable to different ambient and mounting conditions

Slack-wire switch
- Metal enclosure
- 2 Contacts
- 106 mm x 181 mm x 63 mm
- Suitable for heavy duty

Gear-switches
- Metal enclosure with impact-resistant plastic hood
- Various cam shapes for varying switch travel
- Available for easy adjustment of switching points by setting disk cams from front
- Floor side mountable
- Flange for additional mounting on the head
- With groove and feather key to connect onto existing systems
- With Bowex coupling to connect onto existing
- Additional bore 4H12 for pinning
In the Automation technology section, you will find switching appliances for mechanical position detection in various fields of application as well as (safety) sensors with different operating principles; this section also includes a comprehensive programme of command and signalling devices.